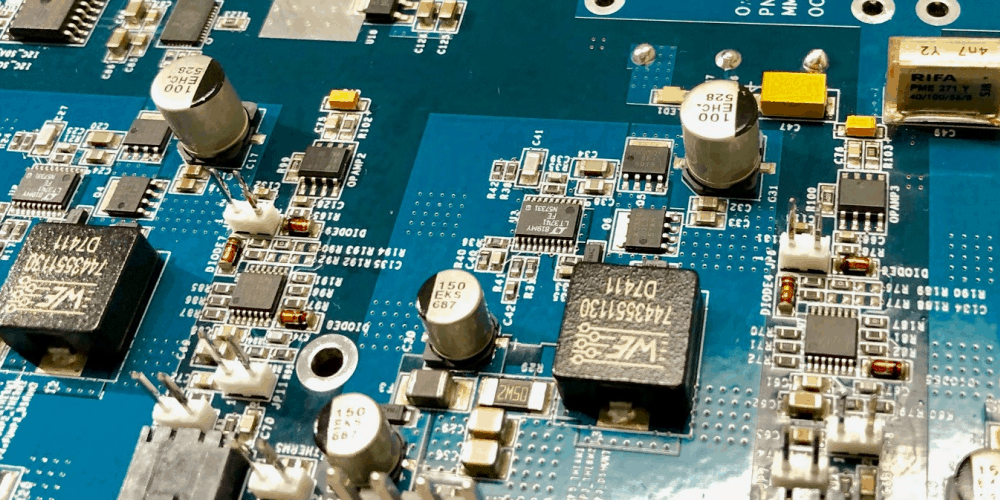
The efficiency of the Printed Circuit Board (PCB) assembly process is crucial in electronic manufacturing due to its significant impact on the overall production speed and product quality.
The necessity for precision and speed in PCB assembly escalates, requiring innovations and improvements in assembly techniques to meet high standards of efficiency and reliability.
Pre-Assembly Preparation
Design for Manufacturability (DFM) is critical in minimize ing PCB assembly times and enhancing the overall manufacturing workflow.
Integrating key DFM practices into automotive PCB, manufacturers can reduce costly reworks and adjustments during the assembly phase.
Essential DFM strategies include simplifying the design, using standard component sizes, and ensuring that components are easily accessible for assembly. These practices not only speed up the assembly process but also improve the durability and functionality of the final product.
Material Selection and Handling
Selecting the right components is fundamental for ensuring the reliability and availability of the necessary parts throughout the production cycle. Effective material selection involves choosing components that are not only compatible with the design but also readily available to avoid production delays.
Proper handling and storage of components are crucial to prevent damage and contamination. Tips for optimal storage include maintaining appropriate environmental conditions and organizing components for easy access and identification during assembly.
Streamlining the Assembly Line
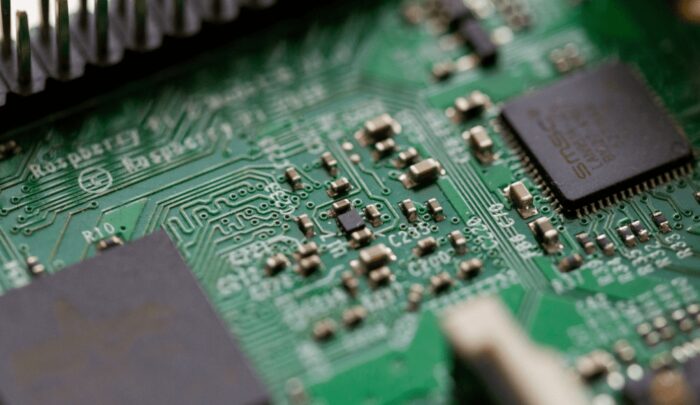
Applying solder paste accurately and quickly is a pivotal step in PCB assembly. Advanced techniques, such as using precision stencils and automated dispensing systems, help ensure consistent and efficient solder paste application.
These technologies reduce the likelihood of soldering defects, which can impede the assembly process. Additionally, the integration of automated systems can significantly speed up this process, allowing for higher throughput without compromising quality.
Placement of Components
The placement of components on a PCB can be performed manually or through automated systems.
While manual placement may be suitable for low-volume or highly specialized assemblies, automated placement machines offer superior speed and precision for high-volume production.
These high-precision machines reduce the likelihood of errors, enhance placement accuracy, and are integral in handling delicate or miniature components, thereby optimizing the assembly process.
Optimization of Soldering Techniques
Reflow soldering is a critical technique in PCB assembly, particularly for Surface Mount Technology (SMT). It involves applying heat to assembled boards in a way that solder paste reflows to create a secure and reliable bond.
Optimizing the thermal profile—adjusting the heating and cooling rates to match specific solder and component requirements—can significantly enhance the efficiency and quality of the soldering process, reducing potential defects and rework.
Through-Hole Soldering
Through-hole soldering techniques, such as wave soldering and selective soldering, are chosen based on their efficiency and suitability for the PCB design.
Wave soldering is ideal for high-volume production with regular through-hole components, whereas selective soldering provides precision for boards with mixed technology, minimizing disruption to nearby SMT components.
Best practices include careful planning of the soldering sequence and setup to integrate through-hole components seamlessly with SMT processes.
Post-Soldering Processes
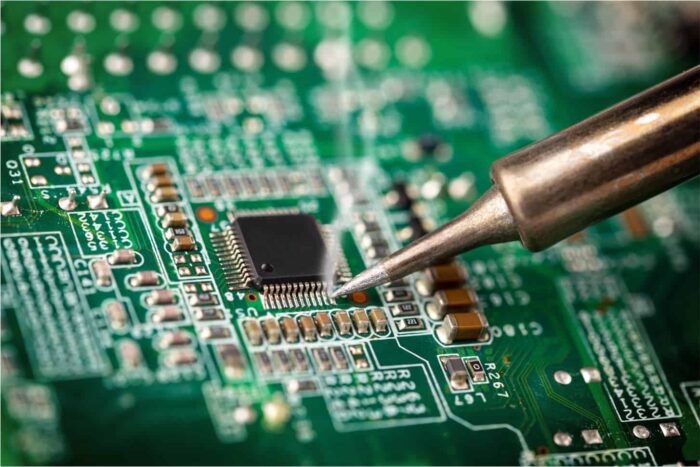
Post-soldering inspection and quality control are essential to ensure the integrity and functionality of the PCBs.
Techniques like Automated Optical Inspection (AOI) and X-ray inspection are employed to detect potential defects such as soldering errors, component misalignments, and circuitry issues.
These inspections are critical for maintaining high standards in PCB assembly, ensuring that each board meets stringent quality criteria before moving to the next production stage.
Troubleshooting and Rework
Even with advanced manufacturing processes, issues can arise during PCB assembly that require troubleshooting and rework.
Identifying common issues quickly and developing efficient strategies for addressing them are crucial for minimizing the impact on assembly time and cost.
Effective rework techniques, such as precise desoldering and component replacement, are necessary to correct defects without compromising the entire board’s integrity.