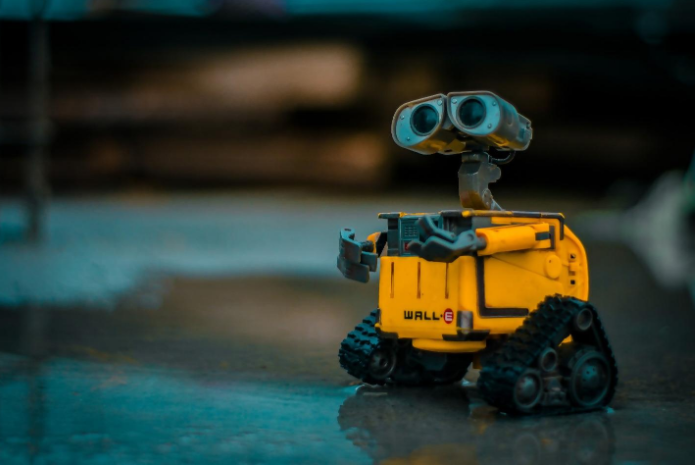
As an engineer, it is impossible to discuss robotics and servomotors in isolation. Servomotors are the heart of all robots and automation systems. You need a servo motor to give whatever it is you are building a breath of life. A robot is dead if it has no heart – servomotors to set it into motion and to precisely control its movements. Due to this fundamental application in robotics and automation, their prices are normally higher compared to other types of motors even though they are not new inventions.
According to Rozum, Servomotors come in all sorts of sizes and design specifications that you can choose from accordingly. The design of different electromechanical systems is possible due to this wide variation. But without servomotors, industrial automation and robot building are just impossible. If you think that I am wrong, then the design engineers will defend my statement.
Talk about RC drones, robots, printers, unmanned aerial vehicles, and many others. All you need for a successful project are servomotors. What do all these applications have in common? Precision! Large robots used in the industries for task automation need super-precision, and that can only be achieved by using this motor.
Servomotors have no substitutes. There is just no shortcut to building a robot or any other electromechanical device without it. Some engineers or engineering students might think about substituting it with its sister stepper motor. That is just impossible.
Stepper motors are quite similar to servomotor with the only difference being that it moves in small definite steps and can only turn up to 180o. This limits its applications in areas where a continuous rotation and more than 180o turn is key.
What is a servomotor, and what makes it the best for robotics and industrial automation?
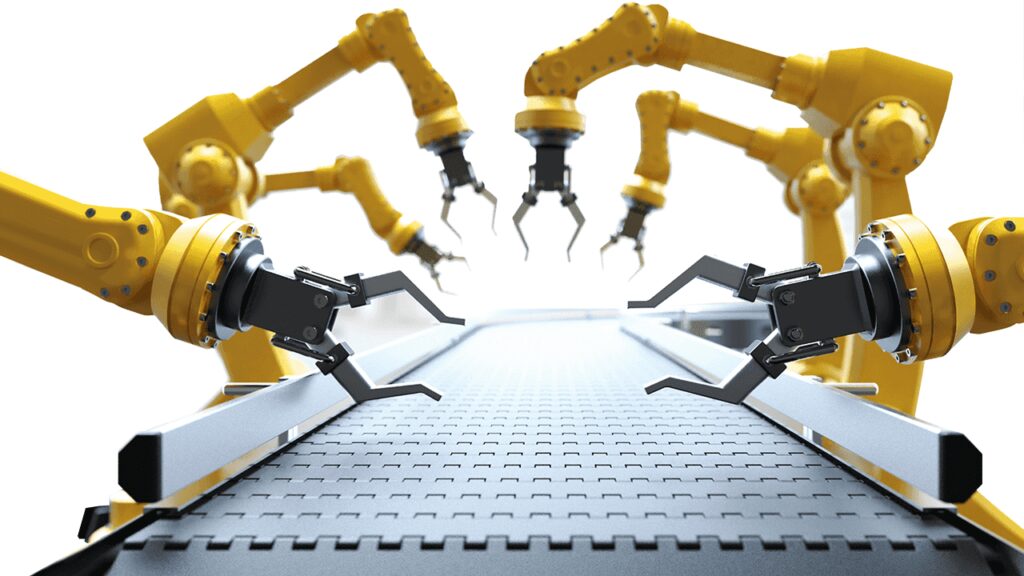
As is already mentioned, servomotors are high-precision devices. This makes it the best in motion control that is key for various industrial processes. For example, there has been a trend in using robots in performing medical surgery. What a disaster would it be if we can’t precisely control the position of these sophisticated yet useful assets!
Apart from the high precision, servomotors come in all sizes and design specifications. This makes it possible to be used in different applications as the selection is not a problem. As a design engineer, you will buy a servomotor depending on the size, torque, and shaft’s revolutions per minute (rpm) needed by your application.
This should be pretty much straightforward as you shall have already determined the expected outcome of your project. For instance, if designing a robotic arm, you shall have it beforehand the design specification such as the maximum weight it can lift. This gives you the torque in Newton-meters required.
What constitutes a servomotor?
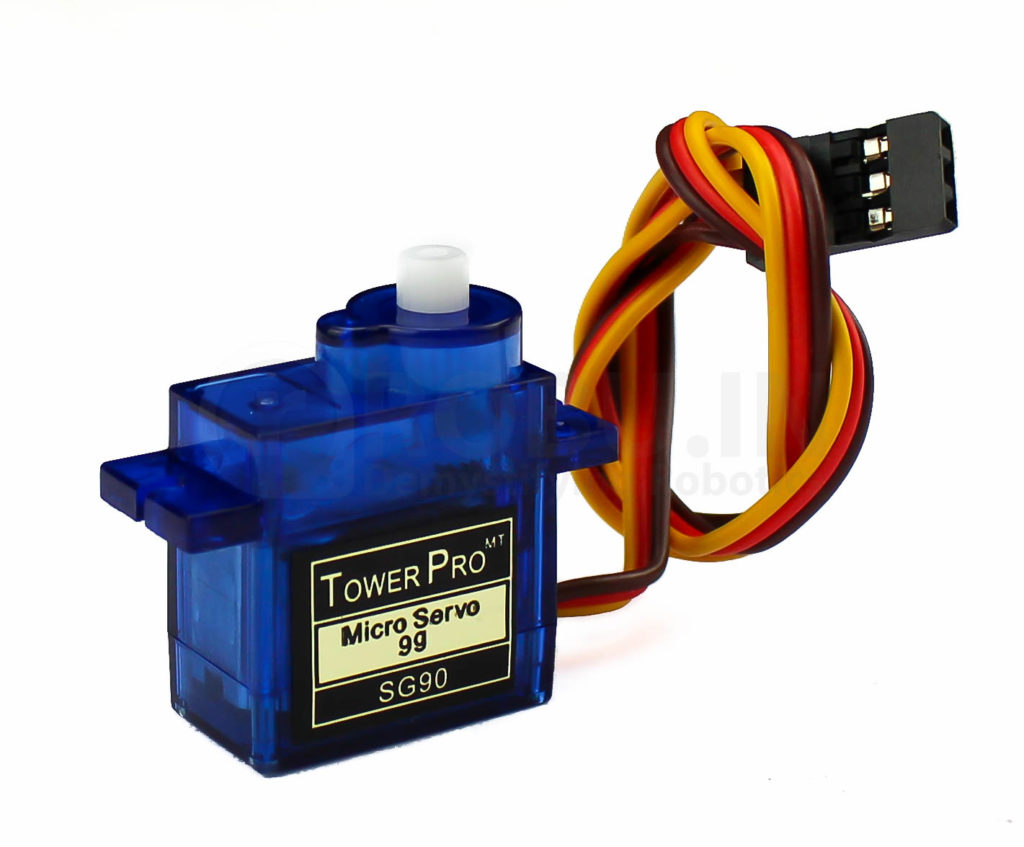
When shopping for a servomotor, you will probably find it in a single package. Within the package are different components that make it be crowned as a servomotor. These are listed below:
- DC or AC motor
- Motion encoder/potentiometer
- Drive gears
- Electronic controller
All these parts are assembled in a single package. DC or AC motor rotates the shaft. The electronic control unit gives an appropriate signal to the motor. The potentiometer is the feedback sensor that tells the controller the angular position of the shaft. Finally, the drive system comprising of a set of gears that outputs the necessary speed and torque.
How is it possible to control servomotors precisely?
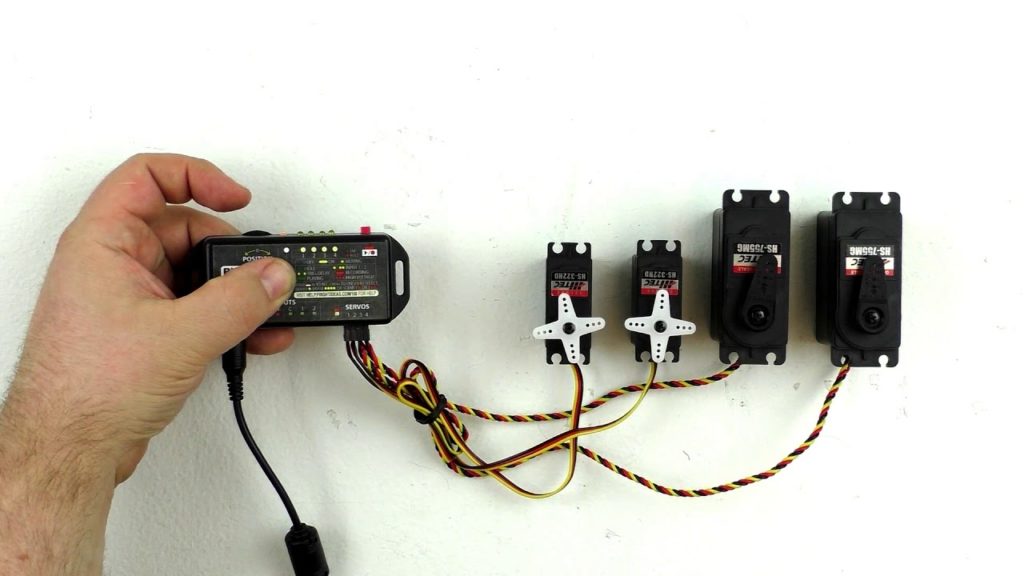
The control signal is from a source that produces electric pulses of different widths. This what is termed as pulse width modulation (PWM). This signal is fed directly to the control input line of the servomotor. Depending on the nature of this signal, the rotate will rotate to the desired position.
When a PWM signal is applied, the rotor will rotate at very high speed This high speed is reduced into a desirable speed with a set of gears while the output torque is increased. The high output torque is responsible for driving the load and also turns the potentiometer, which gives a feedback signal to the controller to determine the angular position of the shaft. The adjustments are made according to this feedback signal to achieve the desired precision.
With the emergence of digital servomotors, there has been an increase in the precision of the angular positioning of the shaft. A breakthrough that led to the emergence of robotic surgeons.
What are the different types of servomotors?
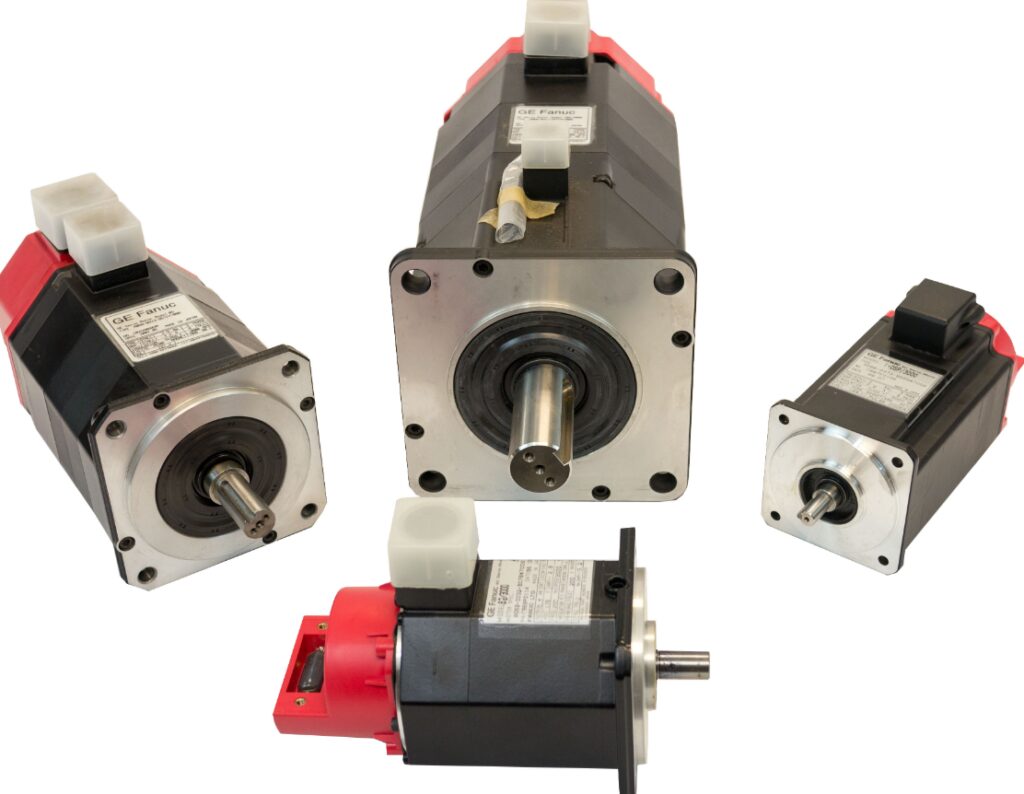
Servomotors are broadly classified into two categories: AC and DC servomotors. AC motor uses a direct current creating force that turns the rotor. DC servomotors rely on direct current for the rotor to spin.
AC servomotors are widely used in industrial automation where we have high current that is characterized by both current and voltage surges. These motors are more immune to the unpredictable voltage spikes in the system.
As you can already guess, DC servomotors are mainly used in the design of electromechanical systems used in small devices such as drones, small robots, toys, and other engineering projects that students handle in their final year of study.
Servomotors. Areas of applications
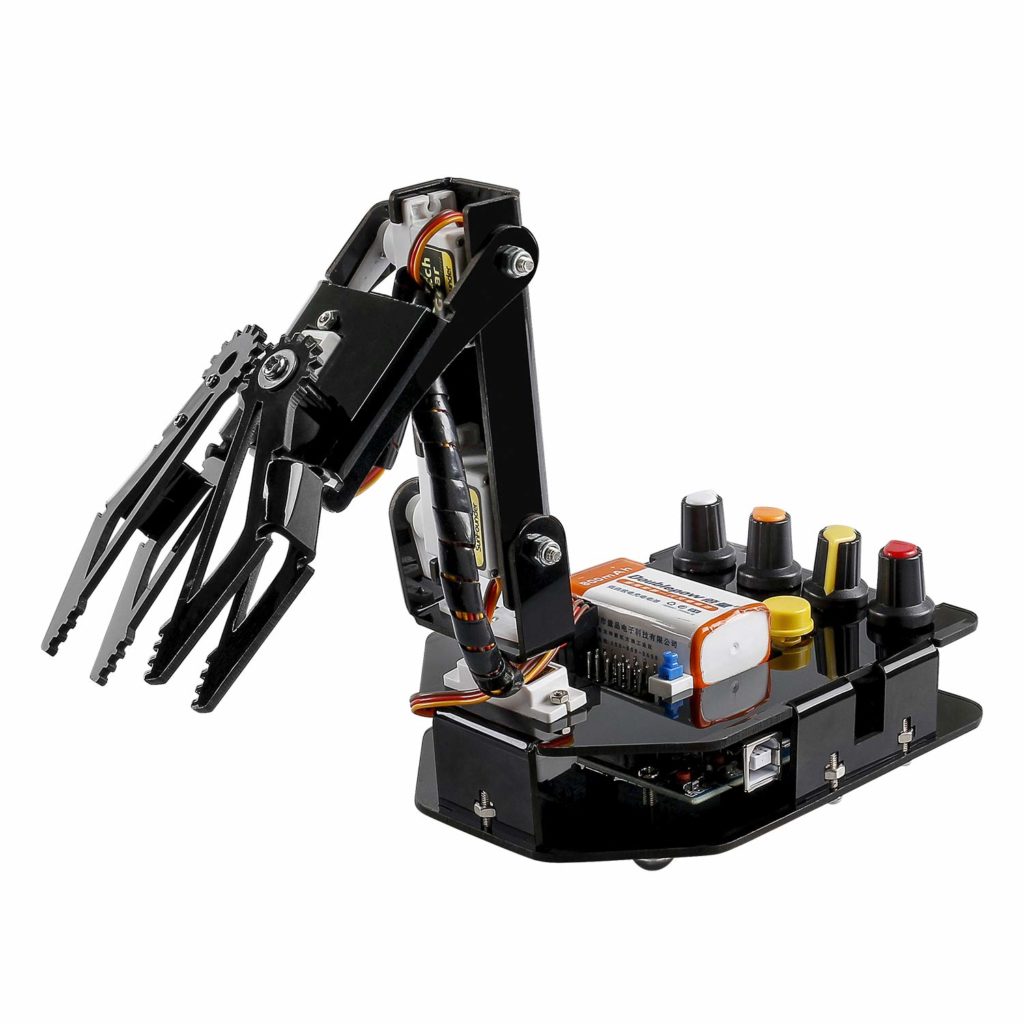
The uses of servomotors are many and cannot be exploited in this small piece. Many applications that achieve meaningful results depend on precise positioning. With just a PWM signal, as discussed above, servomotors can give any desired motion. As such, you will mainly find them in computers, robotics, DVD/CD players, toys, etc. In all these tasks, a repeated action is precisely done in the same manner.
For more insight into the uses of servomotors, let us consider these few cases:
- Design of robotic arm to enable it to precisely move within a defined angle.
- Conveyor belts in the manufacturing industries all depend on the servomotor to successfully move the products from one point to the next without human intervention.
- Cameras depend on servomotor to autofocus an image for a better photographing experience.
- Servomotors are essentially used in robotic vehicles. They drive the wheels to achieve the desirable motions, i.e. start, accelerate, brake, and stop.
- The positions of solar in a solar station are automatically adjusted to get maximum solar energy from the sun using servomotors.
- Milling machines depend on servomotors to precisely cut the sheets in the exact shape and size.
- Textile industries are all automated to perform weaving and knitting by the use of servomotors.
- Automatic doors all use servomotors.
- Computer hard drives use servomotor-controlled heads to write and read data.
- Photocopiers and printers in the offices use servomotors to spin the wheels.
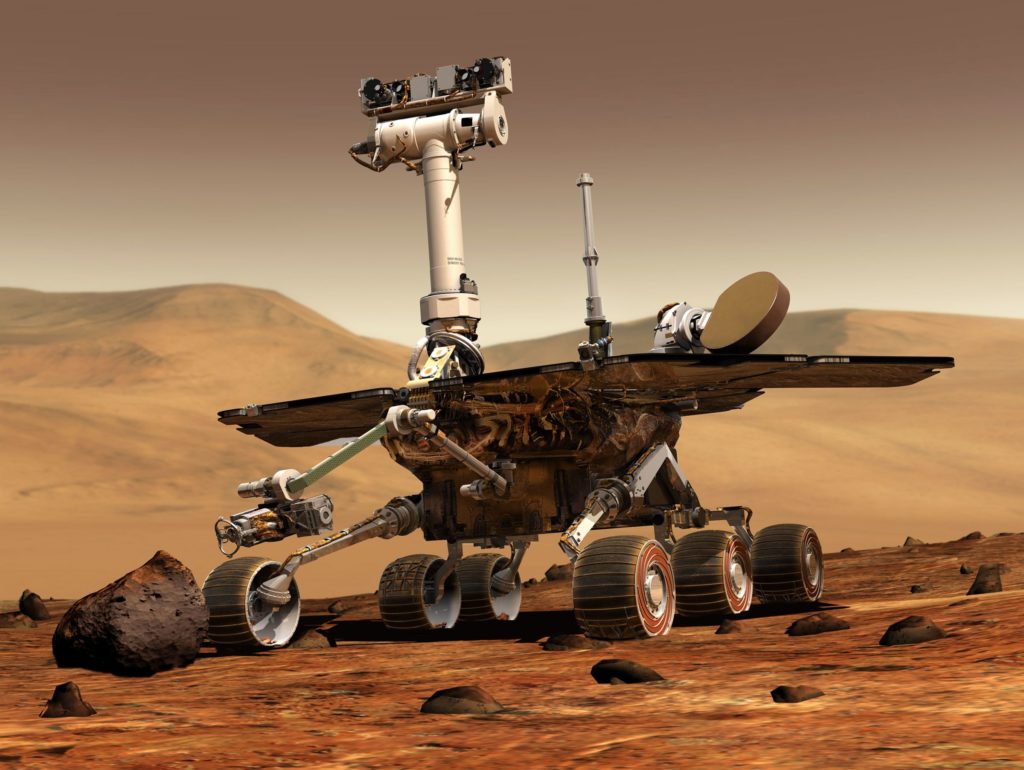
This article was just to give you an idea of what the servomotors are and where they are used. If you are a student engineer or a senior engineer who wants to design any electromechanical system, think about the servomotors first. There is no replacement for it. In fact, you cannot achieve any meaningful industrial automation if you don’t incorporate it into your design.
Servomotors are the backbones of robotics and automation. They are designed to give a precise angular motion, and with the right components, a translation motion can also be achieved. Another positive attribute about these servomotors is that they are easy to control. This makes design and implementation even much easier. It is a breakthrough that drives technology. Much has been achieved with it and even better systems are yet to be built using servomotors.