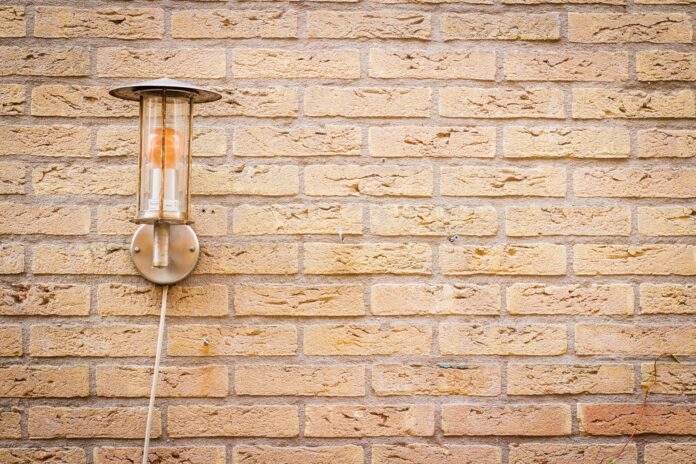
Engineers, architects, and builders depend on the companies that design tools and machines for construction. All companies dedicated to construction need a brick making machine, for example. This makes the work easier and allows a faster building of the structure. It is an essential working tool to have a good performance in the building sector.
That construction companies have a machine to make bricks is the best option.
It creates in little time a solid and durable material made with clay, ash, and cement, among others. The machine can make bricks with different molds and shapes, according to the needs of the structure. This functionality allows working very fast, without losing quality or customization.
Machines, tools, and services are intended to manufacture and design bricks. They contribute to construction from certified electrical components and hydraulic equipment to certified machinery. The objective of a company that produces brick making machines is to facilitate the construction companies’ work. It also assumes various advantages that enhance quality and construction effectiveness.
How does a brick-making machine work?
A machine for making bricks and blocks based on hydraulics usually uses materials such as flying ashes, sand, stone dust, slag, and other raw materials mixed with cement in a reasonable amount, and pressing into brick equipment. To get a visual of the different types of machines, go to eyrconcrete-machinery.com.
A hydraulic brick machine breaks the method of pressing a traditional press from top to bottom and then presses from bottom to top, thus overcoming the deficiency of the old press, that easily erupts and causes damage to the mold. An internal displacement sensor control method has been adopted. This means this kind of work does not affect environmental pollution, and can accurately ensure the size of the brick, so that the product meets the national standard requirements for brick.
Benefits of a brick making machine
The good thing about purchasing an available brick making machine is that it allows a controlled and economical construction. In companies like Rometa, located in Spain, they are very accessible and inexpensive. This results in an excellent investment for construction companies.
Rometa bricks making machines have high, efficient, and reliable production. They operate successfully and produce solid bricks with low-level consumption. These machines drive performance in every operation and brick making.
Each machine is adaptable
Producing bricks with a Rometa machine is a profitable investment for companies. They are capable of creating bricks of coal, ash, clay, waste, and shales for construction. They work with a simple operation that extrudes bricks to size. Capacity, power, weight, and dimension depend on the machine model. Still, their extensive technology manufactures in little time various resistant bricks.
They have high efficiency
All Rometa machines are efficient, operational, and durable in the long term, offering high production capability. A brick making machine is handy and guarantees a long life, making it ideal for businesses. The design has a solid structure and easy maintenance, every month, you can carry out the required technical maintenance.
They are time-saving
Their efficiency is also shown in the number of products/blocks their machines are able to produce within a working day. For example, if an average shift lasts 8 hours maximum, the machine has the ability to produce up to 6000 blocks. And these can be of any type, not just regular bricks, but solid blocks, cobbles, ceiling blocks, curbs, etc.
They offer modern designs
Each mold of the brick making machines can be changed to produce different bricks. According to the power of the machinery, the process of making and building bricks changes. It is recommended that the machine is adjusted to the client’s needs, so the production of the blocks is the most adequate.
Rometa’s different block making machines
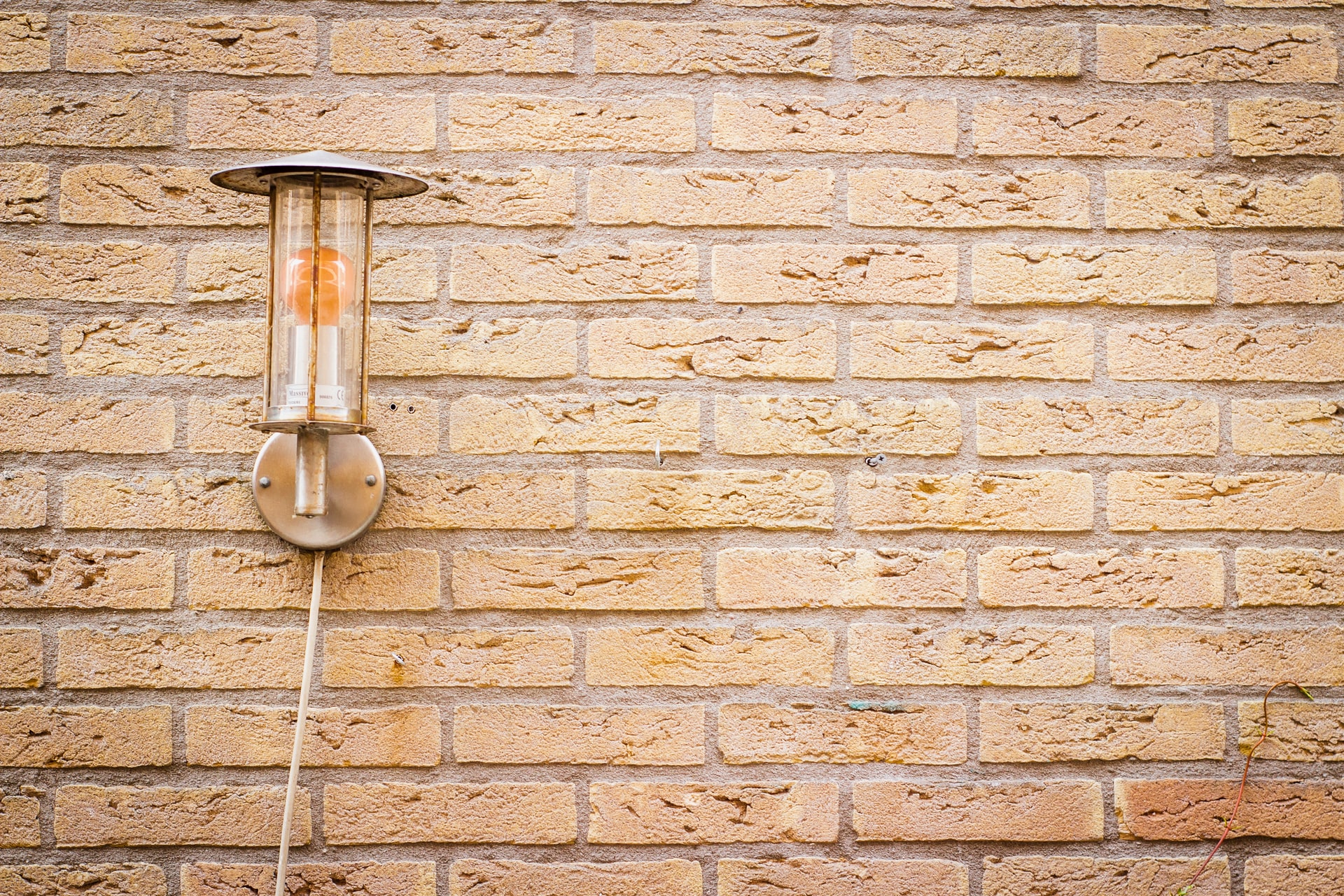
Rometa is a company that distributes brick making machines on 4 continents. It has worldwide recognition and embraces modern technology, providing both a safe installation and training to construction companies. It guarantees operators, supervisors and assistants for easy assembly, installation and operation of the machine.
Today it is the best global company that offers various types of machines, all complying with European safety measures. Rometa distributes and installs excellent machines for making blocks in an automatic, precise and ideal way.
These Rometa machines can make many blocks per hour and makes pieces of different materials, such as concrete. But, what are the most popular brick making machines of Rometa company?
Machine Rometa 1010
The Machine Rometa 1010 has a production of 500 blocks with a short cycle that manufactures up to 4 blocks. It mixes automatically with low capacity compared to the Machine Rometa 4050. It is used for inexpensive constructions that do not require numerous bricks.
Machine Rometa 2010
Produces up to 900 blocks per hour and makes concrete parts, solids and paving stones among others. It is an automatic machine that grants a minimum production of 5,000 and a maximum of 6,000 blocks in less than 8 hours. The highest quality of the Machine Rometa 2010 has 3 configurations adjusted to the level of production. It includes Rometa 2010-10 configuration, Rometa 2010-30 and Rometa 2010-50.
Machine Rometa 2050
It makes up to 12,000 hollow blocks made with any type of material within 8 hours. This machine has a high resistance, with an automatic and palletizing system to guide production. It makes the mix in 3 or 4 hoppers, builds the bricks in each cycle and transports them to the drying area. The Machine Rometa 2050 has a maximum cycle of 18 seconds, depending on the brick’s design.
Machine Rometa 4050
It has an automatic installation that produces up to 22,000 blocks every day. It manufactures approximately 3,000 blocks per hour with materials of concrete and cement. The Rometa 4050 machine has a medium capacity, but a high performance. This way, it creates, doses, transfers, rotates and positions the blocks with programmed control, a robotic and automatic system. It’s a professional machine with a drying area, palletizing, mixer and electronic scale.
What to pay attention to when using the brick making machine
As society advances so does technology, becoming more and more developed. Today the raw materials used in the automatic brick making machines are very common, and their price is not too high. This raw material contributes to sustaining the environment and energy.
We already mentioned some of the advantages of using these automatic machines, but there are many more. For example, their seismic performances are more than good and they have the effect of avoiding ignition. However, when using these machines, there are a couple of things to be aware of:
Before using the electric board, double check if the electricity supply is stable. If you want to check that the real-time anchor bolt is loose, do not vibrate the ground bolt.
Before starting the board, be sure to start the second rotor before stabilizing the electric supply.
When the voltage is not stable, it is caused by another reason. When the machine is switched on, it is necessary to pull the machine out of the speed closing plate in order to prevent damage to the stone material at low speed.
To be precise, an automatic brick-making machine needs to be repaired and maintained throughout the year, so that the life of the electric hob can be extended.
When buying an automatic brick, the user must be optimistic about the quality of the bricks. Do not buy a brick machine with safety hazards. The products we suggested in this article are made by a large manufacturer of automatic brick-making machines. Their quality is absolute. The manufacturer is reliable, and the process is absolutely innovative. And on top of it all, they are present on four continents, making these machines available wherever you are.