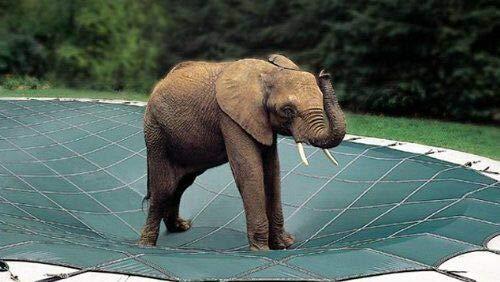
What is the bursting strength of textiles?
Put it simply, bursting strength is the resistance ability to bursting pressure, it describes how strong the textile reacts to applied pressure.
Do common products need to pass the bursting strength test?
Fabrics that must bear weight or withstand forces should be tested with a bursting strength tester, before they made into final products like trailer covers, tarps, trampoline fabric, pool covers, compactor curtains, agricultural bagging applications and etc., to ensure the bursting strength meet the required requirements.
The Widely Used Testing Methods for Textile Bursting Test:
To test textile bursting strength, there are 3 major methods: bursting method, marble bursting method and steel ball method, and these methods are preferred differently based on the textile market. Countries such as the United States, Japan, South Korea, Canada, Australia, etc. use the burst test mainly. In China, a modified test method has also been introduced according to the ISO 13938-1*, i.e. the GB / T 7742.1 “Burst Performance of Textile Fabrics-Part 1: Determination of Burst Strength and Burst Expansion Hydraulic Pressure Method”.
*ISO 13938-1 & ISO 13938-2: 13938-1 Hydraulic pressure source, ISO 13938-2 Pneumatic pressure, according to research from ISO, there appears to be no significant difference in the bursting strength results achieved using hydraulic or pneumatic burst tester, for pressures up to 800 kPa. This pressure range covers the majority of performance levels expected of general apparel. For specialty textiles requiring high bursting pressures, the hydraulic apparatus is more suitable.
Test principle:
The specimen is clamped upon an extensible diaphragm, the liquid pressure is applied under the diaphragm, and the liquid volume is increased at a constant speed and recorded so that the diaphragm and the sample are expanded until the sample ruptures to measure the burst strength.
Before the revision of the national standard “cotton knitted underwear”, the bursting strength was tested by using the marble burst method, that is, a 25mm round marble was used to test the knitted fabric.
The test method listed in the GB / T 19976-2005 “Determination of bursting strength of textiles” standard formulated in 2005 has two differences compared with the previous one: First, the diameter of the marble (steel ball) bursting is changed. It is 38mm, and the second is to stipulate that the strength testing instrument is an internationally-used CRE (constant velocity elongation) strength meter.
Bursting mechanism:
The plain weave will form a rip parallel to the longitudinal direction of the fabric, and there will be more loops detaching along the transverse direction of the fabric. The coil is detached.
Three methods have similar failure mechanisms: Weak Loop Theory
Woven fabric: The deformation of the fabric in the non-warp and weft directions is caused by the two sets of warp and weft yarns shearing each other. The elongation and deformation are greater than in the warp and weft directions. Under the action of the top force, firstly in the direction and strength with less deformation The weakest part of the yarn breaks and then tears relative to each other in the warp or weft direction, so the slit is generally straight.
If the warp and weft deformation capabilities of the fabric are similar, the warp and weft yarns break at the same time when bursting, and the crack is often L or T-shaped, indicating that the warp and weft yarns play the largest role at the same time.
Knitted fabric: The loops are collusion into one piece, and they are subjected to elongation and deformation until the fabric tears.
Non-woven fabric: It is mainly the breakage of fibers and the loosening of the fiber web. The top opening is a bulging loose fiber bag, and the bursting is the loosening of the fiber web.
When the knitted fabric is subjected to bursting pressure, it will cause damage at the weakest point first, and then generate stress set at this damage point. As the test going, the plain weave fabric is damaged. There will be a large number of loops scattered in the horizontal direction, and the slits will continue to expand in the longitudinal direction. The pearl fabric will break more yarns, and the slits will expand around the periphery.
Test Results:
The results of different test methods are compared as follows:
1) The diameter of the steel ball is larger than that of the marble, and the bursting strength obtained by the steel ball method is also greater than that of the marble burst method;
2) The three test methods have similar failure mechanisms, and the shape of the cracks after the fabric is damaged are basically the same;
3) The results of the three test methods have a good linear relationship with each other, and there is a good correlation between the three.
Test significance:
Tensile strength is less suitable for evaluating fabrics like knitted fabrics and lace, that when bursting strength test comes in. When the fabric is damaged, it is often subjected to pressure in the warp, weft, and oblique directions, especially some knitwear (such as weft knitted fabrics) have the characteristics of vertical extension and lateral contraction.
If the tensile strength test is used, the warp, weft and oblique directions must be tested separately, and the burst strength can be evaluated once for the strength of the fabric.
Testing procedure:
For more details of bursting strength tester, please click here.
Instrument calibration:
1. It is necessary to frequently check whether the instrument meets the required requirements and whether all parts of the instrument can work normally.
2. If necessary, standard films such as aluminum foil can be used to verify the comprehensive performance of the burst tester.
3. The elastic diaphragm must be replaced when it is obviously deformed. In the absence of a sample, expanding the diaphragm to a certain height and observe the shape of the diaphragm. If there is a significant difference from the normal spherical crown shape, replace the diaphragm.
4.Clamping of sample
5. Cover the sample on the diaphragm in a flat and tension-free state, and firmly clamp the sample with a ring clamp.
6. Make sure that the sample is not damaged by the fixture when pressurizing.
7. Before the processing test, test the two additional samples prepared in advance according to the above regulations, and observe whether the burst strength of the fabric until the breakage is completed within the specified time range. If not, the pressure rate should be adjusted according to the conditions of the instrument so that the average bursting time is within the specified range. The general fabric is specified as 30 ± 10s, and the wool fabric is specified as 15 ± 10s.
8. For the deterministic test, use the adjusted pressure rate to test the samples one by one, and record the burst strength and burst expansion of the sample. If the specimen breaks at the edge of the ring of the fixture, another specimen shall be taken and redone.
9. Diaphragm correction number Use the same fluid speed as the above test. In the absence of a sample, clamp the diaphragm with a clamp to expand the diaphragm to the pressure required for the average expansion and expansion of the sample. The pressure is the number of diaphragm corrections.
Test Result Valuation:
1. Calculate the burst strength of each sample, that is, the total pressure of the burst sample minus the pressure required to deform the film.
2. Report the burst strength of each sample and the average burst strength of the batch and laboratory samples.
3. Report the type of instrument used for the test.