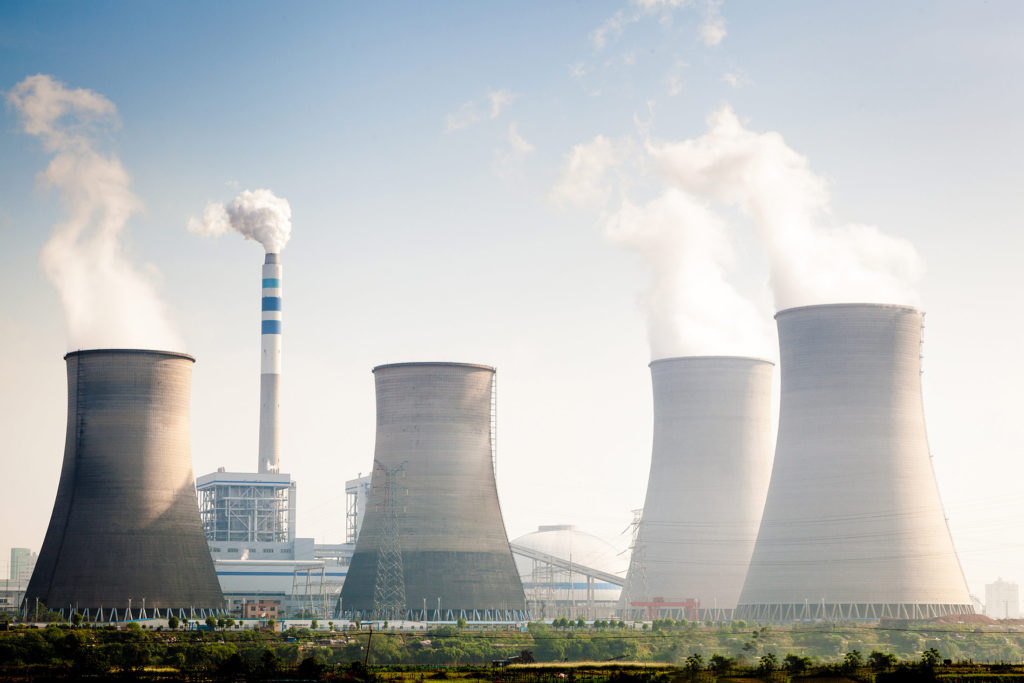
Cooling towers are found in industries where process cooling is required, such as chemical processing, power plants, steel mills, oil refining, waste incineration, and almost all the manufacturing companies. Cooling Tower works as a heat exchanger. A cooling tower uses evaporation, a natural process to exchange waste heat produced with all the workings of the industry into cooler water, which gets reused in the industry again.
The whole process is done by forcing in the air with a cooling fan and water so that it comes into each other. Cooling towers come in different sizes and different designs. They are classified by air direction (crossflow or counterflow, types of the draft ( mechanical and natural).
Regardless of their classification, they all do the same primary function of exchanging heat in the most effective way.The need to reduce the consumption of water, cost, and energy is the need of the hour and guided by laws in many places. This can be done by an efficient cooling tower. Industrial Cooling Solutions helps you with repairing, maintaining, and upgrading your cooling towers.
This post will help in getting an idea about a few of the most known cooling tower issues seen, which will help better take care of your industrial and commercial property. Great business begins with decent spending that incorporates holding the fixed cost down. A piece of each business is suffering a heart attack and agreeable spot for clients and customers to work together in.
Huge business properties highlight cooling towers that should cooperate to keep the working spaces cool and happy during the summer especially during the hot days. It is critical to realize the regular cooling tower issues and answers to help monitor your spending plan.
To keep the cooling tower effective, it is required to keep it in proper conditions.
There are 4 most common problems regarding cooling towers. Let’s look into them and know what should be done to fix them.
- Corrosion
- Biological Contamination
- Scaling
- Fouling
There are four significant kinds of treatment of water issues that component cooling towers should monitor. These are corrosion, fouling, biological contamination, and scaling. These issues decrease the cooling pinnacle’s capacity to be energy-productive as planned. This implies they take greater power to do similar work.
1. Biological Contamination

The normal and copious supplements that most of the water sources contain, is an ideal spot for the development of undesirable biological development, like microorganisms.
These pollutants aren’t useful for individuals and are more awful for the effectiveness of the cooling tower. They come as biofilm, that is a development on the inner segments of the cooling tower. Indeed, even meager layers can diminish warm proficiency drastically.
2. Corrosion
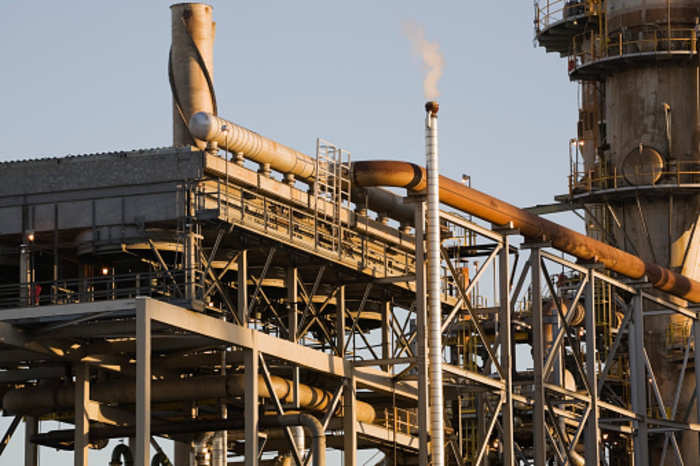
Water corrodes almost everything, especially metals, over a period of time. Water combined with all the industrial chemicals makes cooling towers more prone to the problem of corrosion.
Corrosion is basically caused by the combination of sodium, air, and many more chemical compounds found in the water. This chemical compound reaction causes the loss or destruction of metal within the cooling tower.
If preventative techniques and solutions are not taken for corrosion, it can be dangerous for the safety and the efficient working of the cooling tower, which results in an increase in the energy cost. If safety measures for corrosion are not taken within time, it can cause a lot of destruction and can be a costly affair to repair.
3. Scaling
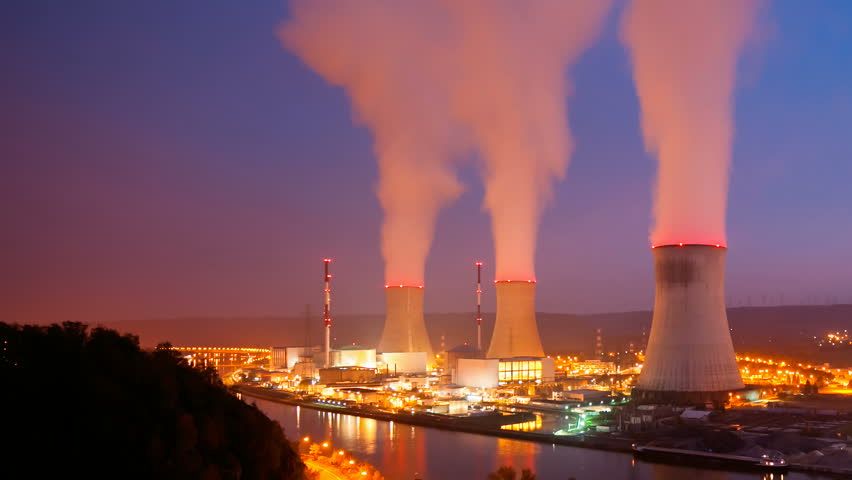
The essential job of a cooling tower is to trade heat from industrial processes or the chiller. This implies that the development of minerals in the water can make layers that ransack effectiveness.
The various sorts of minerals, like calcium and others that are important for the high warmth framework, separate and are stored on the heat trade of cooling tower’s surfaces. Scaling should be taken out, or working costs will increment.
4. Fouling
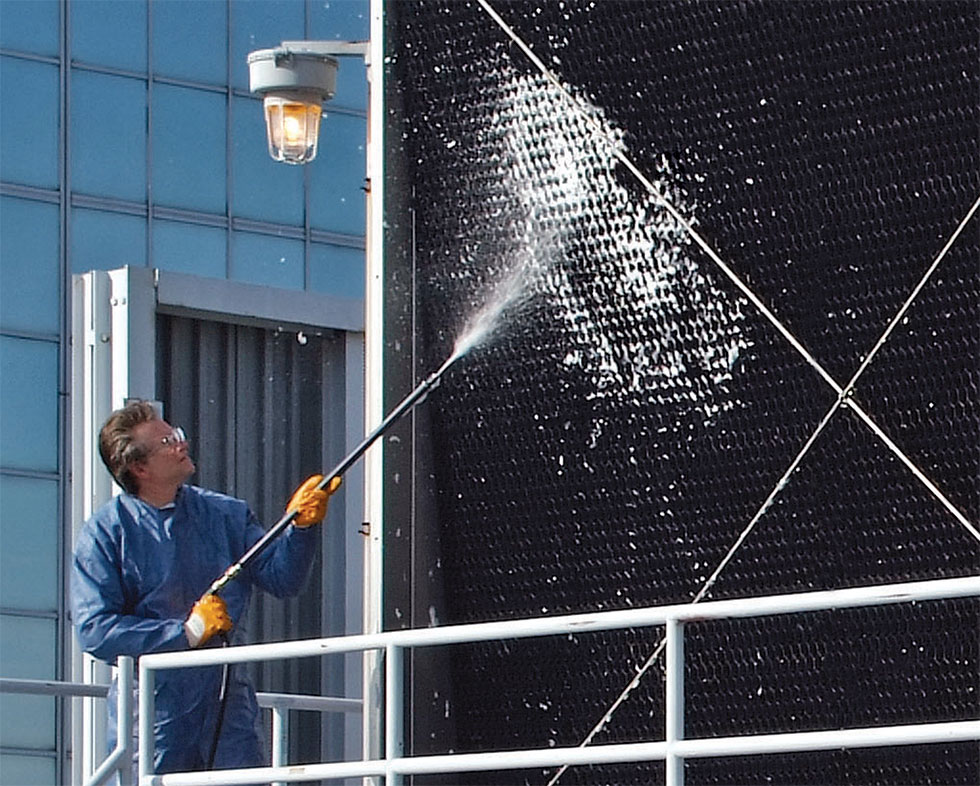
Fouling can happen in various spaces of your cooling tower framework. The clogging of cooling surfaces or lines with garbage, soil, and the residue is known as fouling. At the point when water can’t make it into and go through the fill as planned, the air isn’t cooled as expected. This implies that the framework needs to work longer to accomplish similar outcomes. Which implies it is utilizing greater power.
Solutions to Fix The Cooling Tower Problems-
The maintenance of cooling towers is a customized and progressive process. There are different solutions for different problems seen in cooling towers.
Choosing the best company for cooling tower maintenance will help you control all these four major problems with lower repairing costs. Let’s check various solutions that help in solving the above-mentioned problems.
Treating Biological Contamination
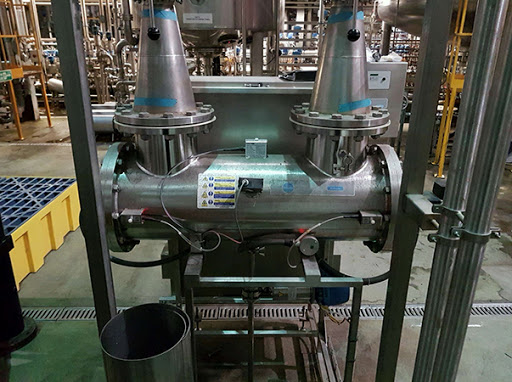
Biological contamination, if seen in your cooling tower, the first important step is to take the water sample. With the help of the sample, it can be told what treatments are needed to be taken for the cooling tower.
Corrosion Prevention
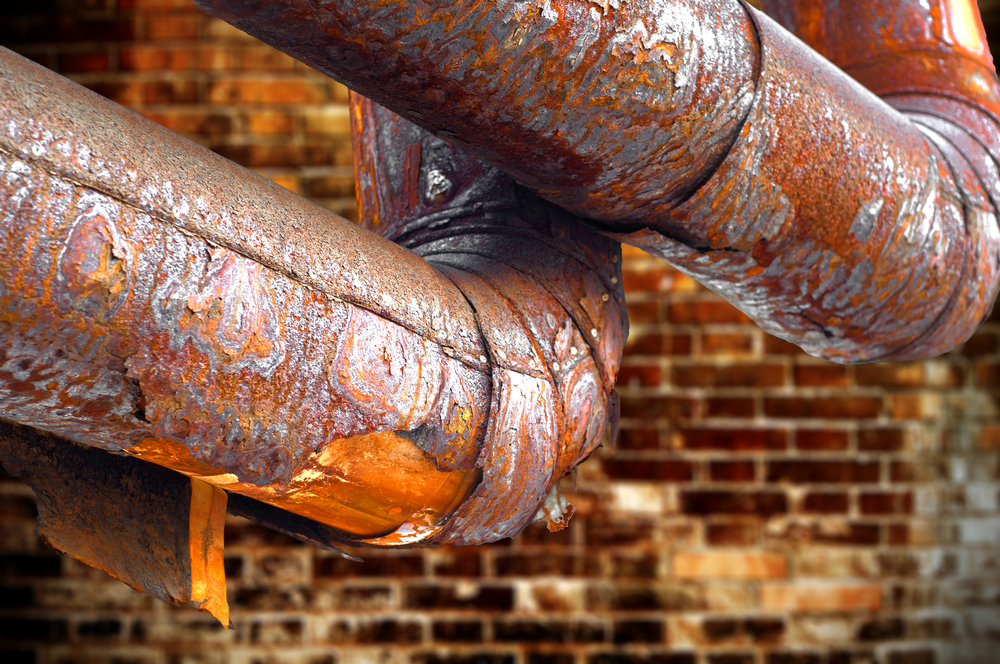
There are three different ways with the help of which corrosion can be controlled, that is by coatings, adding orthophosphate to the water, or by raising the water pH to 9.0. A sensitive equilibrium of these methodologies can help broaden the existence of your cooling tower and the individual parts.
Fouling Treatment
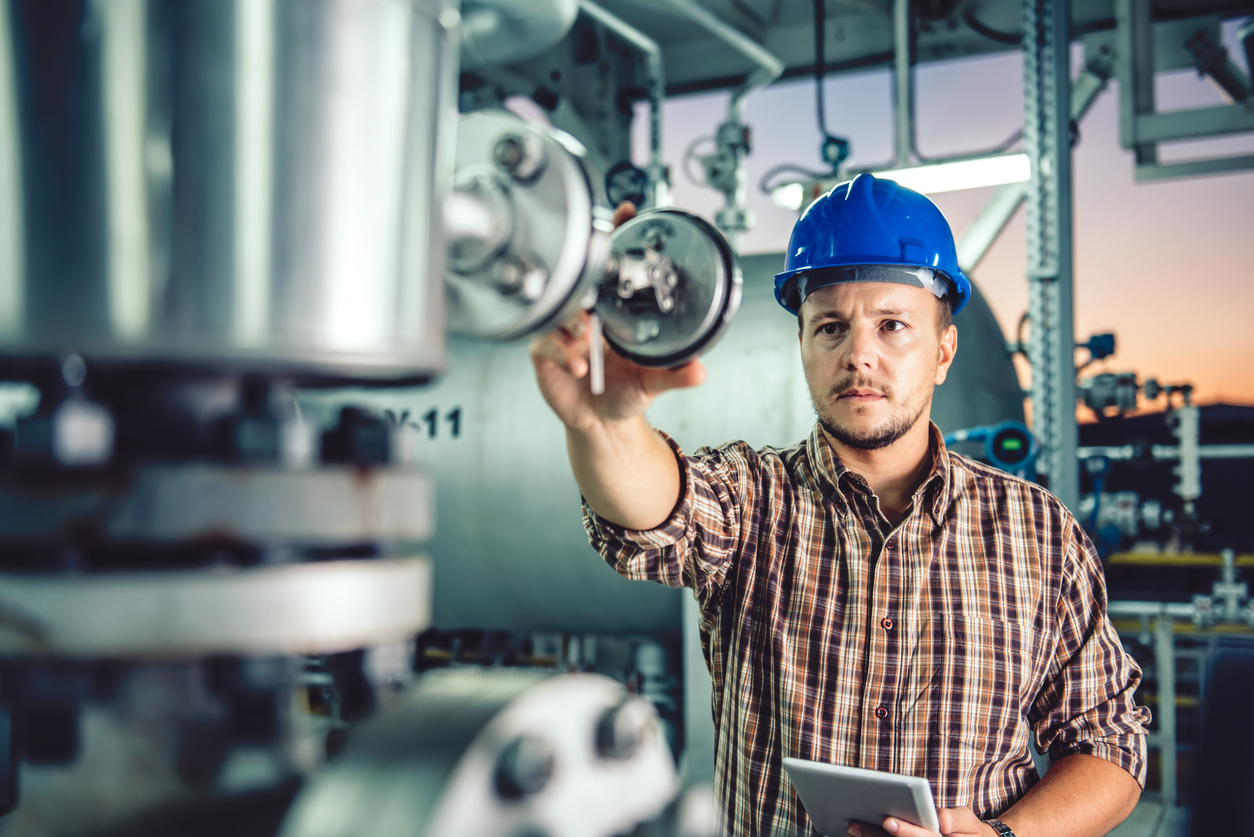
Fouling in the cooling towers can cause decreased performance of cooling towers that can lead to inflated consumption of energy. Fouling does this when biological matter forestalls the even dissemination of water through the framework in tubes, spouts, fill, or different zones where water needs to have unrestricted development.
With the help of chlorine, Fouling can be treated, changed in the fill, and spouts or other equipment can be traded out for new parts to recuperate the exhibition cooling tower.
Remove the Scaling
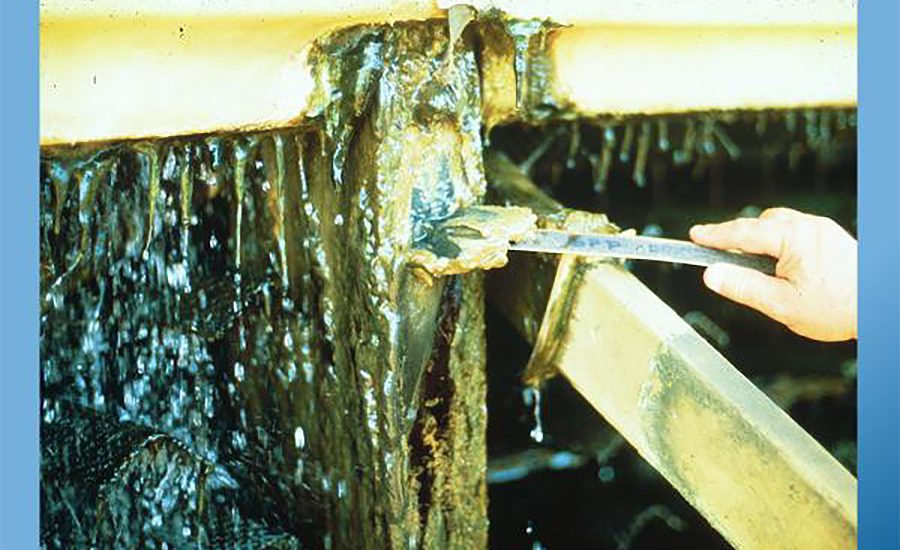
A thin coating of chemicals or minerals that damages the tube and prevents the effects of the cooling towers is known as scaling. Scaling can cause a reduction in heat transfer, restrict proper power generation, and increase backpressure. The main reason and cause of scaling is calcium, which needs to be treated and monitored from time to time.
The tube coatings made with polymers are one way to prevent scaling. The polymer coating maintains the performance of the cooling towers by providing a surface that is conductive to industrial heat generation and also provides protection against calcium by not allowing it to stick and build up on the surface. Another way of removing scaling is by using different procedures for cleaning. After the cleaning, it’s better to put up a coating of the chiller.